Category Archives: Post
Shaker Screen Shipped to European
TR Solids Control is a professional and well-known supplier of all kinds of shaker screen in China. At this week, we completed a new batch of pyramid shaker screens at our workshop. Now they are ready for shipping to European. What’s more, they are along with wedges of Mongoose screen. All of these spare parts will install on Swaco shale shaker in client’s oil drilling field.
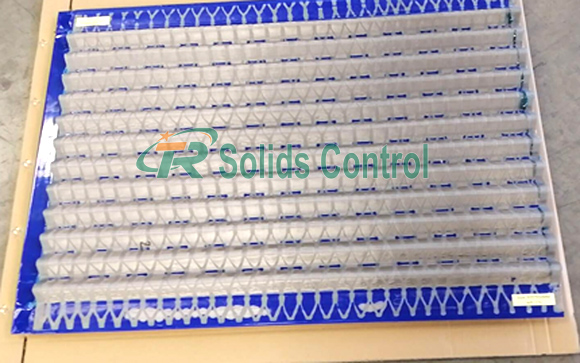
VSM 100 replacement shaker screens are ready for shipment.
The size of this PMD shaker screen is 920*635*28mm. They will be used for Swaco VSM100 shale shaker. TR shaker screens are popular with more and more users. Our shaker screen mesh ranges from API 20 to API 325. We are confident with high quality and performance of our shaker screen. The reliable and stable quality is from high quality raw material, strict technique process and inspection.
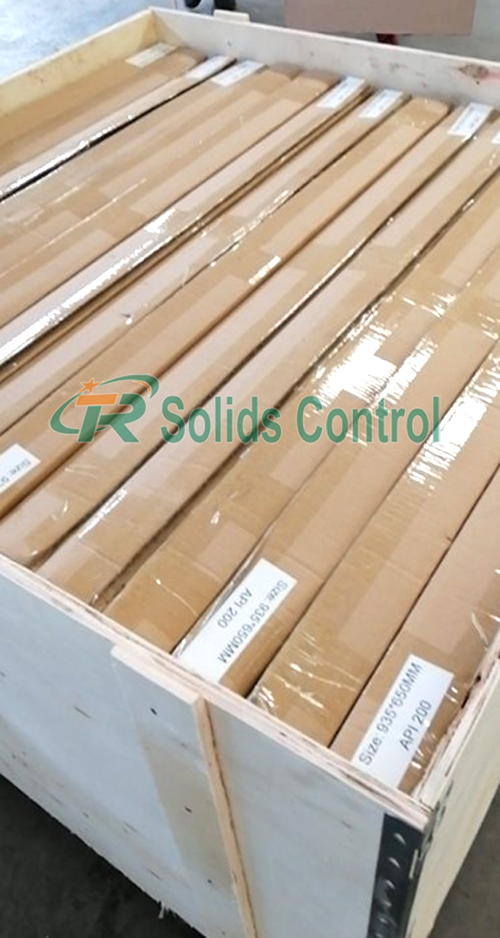
PMD shaker screens packing.
Are you finding a stable supplier of shaker screen? Please feel free to contact TR Solids Control for any demand or question. Customer satisfaction is our highest pursuit. Meanwhile, we supply solid control equipment such as mud agitator, shale shaker, mud cleaner, desander, desilter, centrifugal pump, shear pump, decanter centrifuge, flare ignition device, jet mud mixer, vacuum degasser, etc. Contact with us for free quote!
Working Principle of Centrifuge
What is the working principle of centrifuge? Let’s start with what centrifugation is.
Centrifugation is the use of centrifugal force produced by the high-speed rotation of the centrifugal rotor to accelerate the settling speed of particles in the liquid and separate the substances with different settling coefficients and buoyancy densities in the sample. Therefore, it is necessary to use strong centrifugal force to force these particles to overcome the diffusion and produce sedimentation movement.
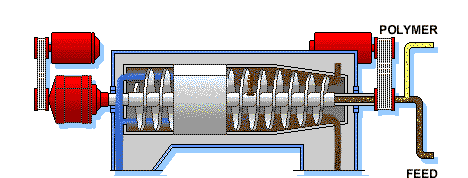
There is a cylinder rotating at high speed around its axis, called a drum, which is usually driven by a motor. When suspension (or emulsion) is added to the drum, it is rapidly driven to rotate with the drum at the same speed. Under the action of centrifugal force, each component is separated and discharged separately. Usually, the higher the rotating speed of the drum, the better the separation effect.
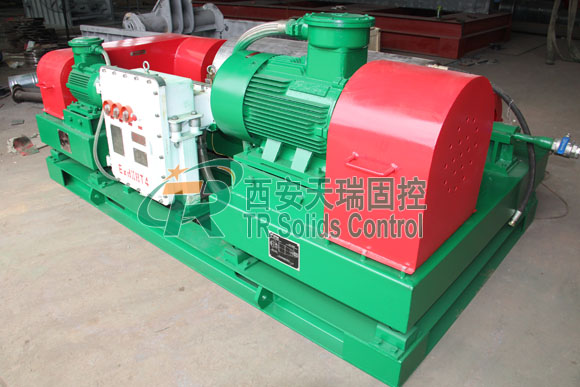
According to the structure and separation requirements, industrial centrifuges can be divided into filter centrifuges, sedimentation centrifuges and separators.
Filtration centrifuge: centrifuge for centrifugal filtration, centrifuge relying on filter screen and centrifugal force.
The working principle of the filter centrifuge: there are many small holes in the wall of the drum, there is a filter screen (filter cloth) in the wall, the suspension rotates in the drum, and the liquid phase is thrown out of the screen by centrifugal force, while the solid particles are intercepted by the screen, forming a filter cake, thus realizing the solid-liquid separation.
Scope of application: suspension with high solid content and large solid particles (d > 10 um).
Settlement centrifuge: A new type of horizontal screw discharge centrifuge, its working principle is to use the difference of solid-liquid specific gravity, and rely on the centrifugal force field to expand it thousands of times, the solid phase is settled under the centrifugal force, so as to achieve solid-liquid separation, and discharge the body separately under the action of a special mechanism.
The working principle of sedimentation centrifuge is that there are no holes on the drum and no filters. The suspension rotates at high speed with the drum, and different centrifugal inertia forces are produced due to the different proportion of solid and liquid phases. Solid particles with large centrifugal force are deposited on the inner wall of the drum, while liquid phase is deposited in the inner layer, and then separately discharged from different outlets to achieve the purpose of separation.
Scope of application: less solid content and smaller solid particles (d < 10 um).
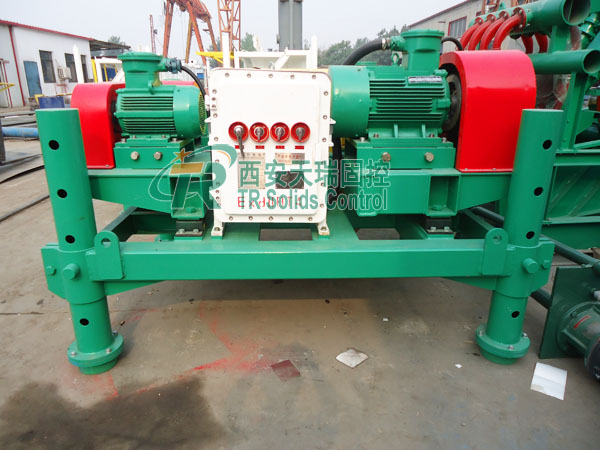
Above is the detailed introduction of the working principle of centrifuge, we must understand these principles, in order to better use the practice.
Contact us
Sunny Lee | Sales manager
M(WhatsApp): +86 13186019379
EMAIL: sunny@trsolidscontrol.com
TR Solids Control wish you Happy New Year
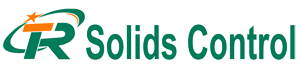
To wish you joy at this holy season.Wishing every happiness will always be with you.Good health,good luck and much happiness throughout the year!May the joy and happiness around you today and always.Please accept my sincere wishes for the new year.I hope you will continue to enjoy good health.May the coming New year bring you joy,love and peace.Season’s greetings and sincere wishes for a bright and happy new year give you endless brand-new good wishes.Please accept them as a new rememberance of our lasting friendship!
Sludge Dewatering System
Technical Parameter
Model |
TRWNT-20 |
Oven dry sludge capacity |
300~600kg/h |
Solid content in sludge |
10000~20000mg/L |
Sludge capacity |
18~24 m3/h |
Clear liquid solid content |
0.03% |
Inlet ludge water content |
75~80% |
Outlet Sludge water content |
Less than 30% |
Electricity consumption |
4.4kw/h |
Flushing water consumption |
80L/h |
Addition Rate of Polymer Flocculant |
DS ~0.8% |
Maintaining management frequency |
5min/day |
Water supply pressure |
0.1~0.2MPa |
Net weight |
3500kg |
Operating weight |
4550kg |
Setting environment
Temperature Scope of Application |
-10℃ ~ +40℃ (No ice.) |
Applicable range of humidity |
Max. 90%RH (No condensation) |
Height |
Below altitude 1000m |
Supply voltage |
Three-phase 380V 50Hz |
Water supply pressure |
0.1~0.2MPa |
※ This Sludge Dewatering System belongs to indoor specifications. Please set it indoors.
※ Please set it up according to the specifications and drawings.
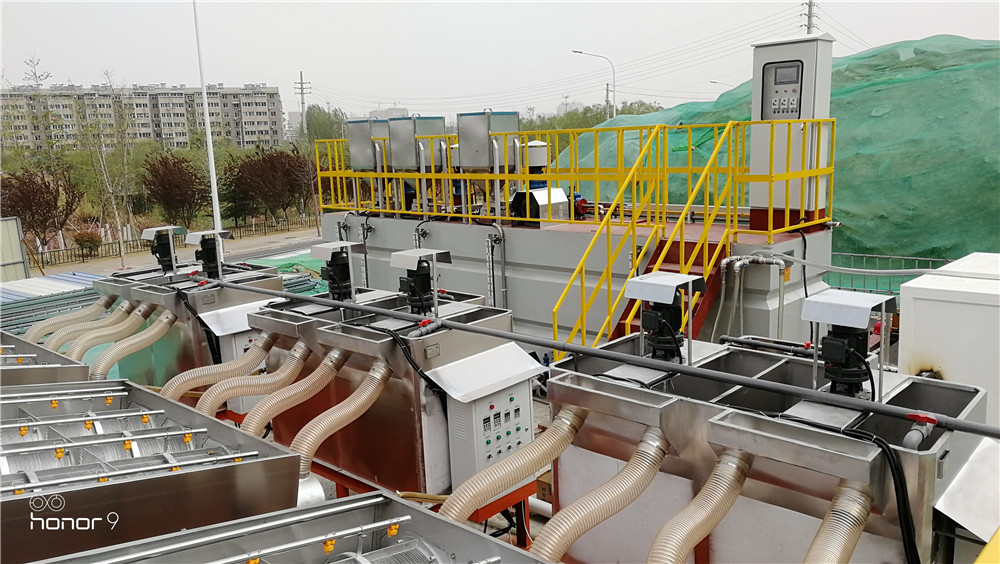
Sludge Dewatering System
Diameter parameters of each pipe
Sludge Conveyor inlet |
DN100 |
Pharmaceutical liquid delivery port |
¢25 |
Filtrate outlet |
DN80 |
Water supply outlet |
¢25 |
Return flow |
¢100 |
Mixed flocculation tank emptying |
¢63 |
Contact us
Sunny Lee | Sales manager
Maintenance of Shale Shaker Vibration Motor
Maintenance of Vibration Motor:
-
Clean the dust on the casing regularly.
-
Before using, it is necessary to check whether the fixing bolt of the vibrating motor is loose or not. Otherwise, it must be tightened before it can be used.
-
Check whether there are friction, buried pressure, squeezing and other phenomena in the cable introduced by the vibrating screen.
-
Good lubrication should be guaranteed during the operation of the vibrating screen motor.
A suitable amount of LGHP2 high temperature grease specially designed by SKF company. It was filled in the inner space of the bearing before the motor was assembled. Tthe applicable temperature was -40~200 C.
The LGHP2 grease is supplemented once with a refueling gun for every 2000 running hours. The amount of the grease in each bearing is not more than 25.8g.
If the average daily temperature rise of bearings is found during 2000 hours (temperature rise refers to the measured temperature of the bearing position of the motor housing minus the ambient temperature, which requires that the temperature rise of bearings be monitored every half-month), it is possible that the bearings may not be lubricated enough by floating above 10 C. At this time, the lubrication period and the amount of supplementary grease should be reduced at the same time as appropriate, and in principle, it should be kept in each bearing every 2000 hours interval. The total amount of grease supplement is not more than 25.8g. For example, when the lubrication cycle is half as normal (1000 hours), the amount of supplementary grease is no more than 12.9g. The average daily temperature rise of bearings is reduced by half at the same time for every 10 C lubrication cycle and the amount of supplementary grease.
In order to ensure the normal operation of bearings, LGHP2 high temperature grease must be used, and the oil injection hole should be wiped clean before adding fresh grease.Normally the bearing will have a natural temperature rise for one or two days after just lubricating or re-lubricating.In order to prevent dust from entering the oil injection hole, damaging the bearing and sealing the oil injection hole with oil cup in peacetime.
5. Insulation measurement of motor windings should be carried out when the equipment is used after a long period of downtime. Measuring insulation resistance with 500V megohmmeter should not exceed 0.5MSZ before it can be used.

Shale Shaker with Vibration Motor
Contact us
Sunny Lee | Sales manager
Effect of Screen Surface Structure of Mud Shale Shaker on Solid Phase Control
Mud Shale Shaker
Mud Shale shaker as a first-class solid control equipment, the relative movement between the screen surface and drilling mud is a necessary condition for screening. In screening machine, the movement of drilling mud to screen surface mainly includes vertical movement and movement.
The structural parameters and movement properties of the screen surface of the mud shale shaker, the ratio of the screen hole area to the total area on the screen surface is called the opening rate. The larger the opening rate, the higher the screening efficiency and productivity of the mud shale shaker. Therefore, the screen surface mostly adopts square sieve hole, but it is better to use circular hole when the water content is high and the particle size is small.
The screen surface of mud shale shaker which moves vertically is not easy to be blocked by drilling mud, the looseness of the layer is increased, and the segregation rate is also high. The movement frequency and vibration amplitude of the screen surface also affect the movement speed of drilling mud particles on the screen surface and the probability of passing through the screen hole, which has a great influence on the screening efficiency, and the screening of drilling mud is not complete.
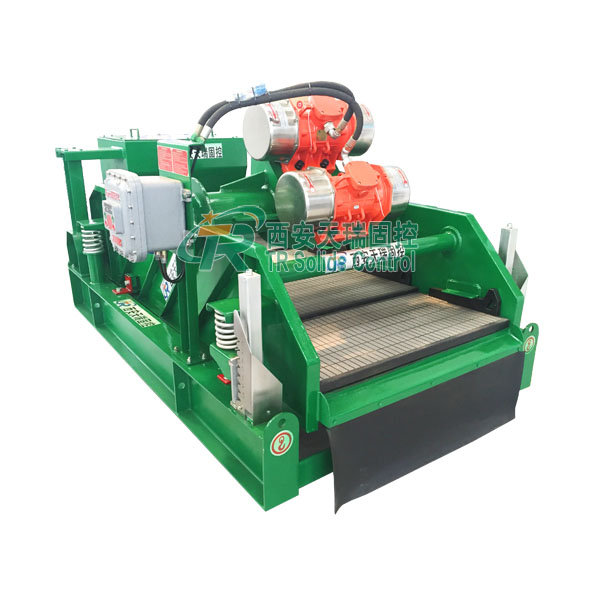
TRZS585 Mud Shale Shaker
In view of these problems and combined with the situation on the spot, we can do the following several coping strategies:
1. Increasing the screening rate of mud shale shaker screening can adjust the feeding mode. Without careful consideration of the spatial location of the site, the feeding is not along the full screen width, which will inevitably result in the inadequate utilization of the screen surface.
2. Under the condition of permissible field conditions, adjusting the inclination angle of mud shaker can be considered. Appropriate inclination angle is beneficial to reducing the thickness of drilling mud and realizing thin bed screening.
3. How to improve the opening rate of the screen plate of the shale shaker screnn. High opening rate is beneficial to improve screening effect. Usually, high opening rate of stainless steel welded sieve plate can be paid attention to.
4. To reduce the porosity of sieve paste, self-cleaning sieve plate, such as spring rod sieve surface, can be considered.
5. For dry screening, the feed moisture should be strictly controlled. When the water content is high, the ingredient screening can be considered.
6. Wet screening, if conditions permit, is the most effective means to improve the screening effect.
7. If conditions permit, a fixed sieve is added at the feeding end and a rough sieve is carried out, then a double or triple mud shaker can be used.
Contact us
Sunny Lee | Sales manager
Solution to Over-fast Damage of Shale Shaker Screen
There are many main reasons for the quick breakage of mud shale shaker, such as unqualified shaker screen quality, tension of shaker screen, wrong steering of vibrating motor and accumulation of clay, which will lead to the quick breakage of mud shale shaker. In order to solve these problems, how should we avoid and make timely adjustments?
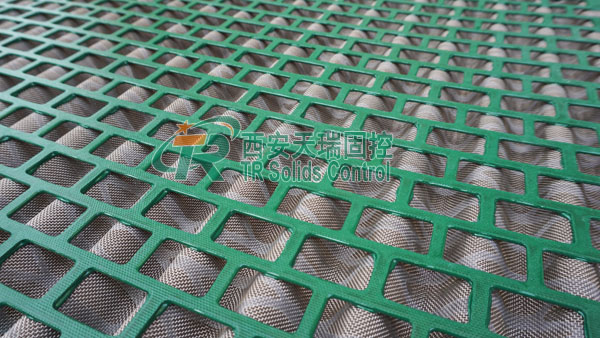
Shaker Screen tension is insufficient to cause screen tremor
Shaker Screen tension is insufficient to cause screen tremor
Shaker Screen tension is insufficient to cause screen tremor, which is usually broken or damaged along the edge of the screen or at the edge of the blanking press strip; screen quality is not up to standard, the screen generally has upper sieve stratification and lower stress layer, requiring that these two layers closely adhere to each other, if the pre-tensioning process is poor, when the bottom of the screen is subjected to.When the force layer is tightened, the layering of the screen is not tightened, and the throwing force of the drilling cuttings decreases greatly when the drilling cuttings are working, so that the drilling cuttings can not be discharged. When the vibration motor steering is wrong and vibration motor steering is debugged, the field operators consider that as long as the drilling cuttings go forward, the method is not suitable. Used for translating elliptical shaker.
The motor rotates inward incorrectly
If the motor rotates inward incorrectly, the projection angle is also forward, but the cuttings have the force of rolling backward. At this time, the speed of the cuttings moving forward is much slower. And the time spent on the screen is long, even the cuttings can not be discharged. How to effectively solve these problems: when the screen box is running, press the stop of the electronic control box.
At this time, the vibrating screen will stop slowly, observe the elliptical track formed by the small points on the side plate when the vibrating screen is running, roll to the sand outlet for correct turning; remove the shaker shield, check whether the apricot eccentric block rotates outward; change any two phase lines in the power supply of the electric control box, and sprinkle some sand on the screen. One of the quicker sand removal speeds is the right direction.
When drilling cuttings accumulate on the screen and quickly damage the screen, we should increase the vibration amplitude
- When drilling cuttings accumulate on the screen and quickly damage the screen, we should increase the vibration amplitude;
- Use spraying water to wash the screen and drilling cuttings to reduce the stickiness of the drilling cuttings, but this method is only suitable for situations where water is allowed to be added;
- Adjust the angle of the screen at the end of the sand outlet to downward, which is conducive to the discharge of cuttings by gravity, but may lead to slurry runoff;
- Changing the mesh number of screen or adjusting the flow rate of single screen to ensure that the flow stop point of drilling fluid is close to the outlet of screen, and drilling cuttings can be discharged smoothly under the lubrication of drilling fluid.
These are only part of the rapid breakage of the screen screen and the corresponding treatment methods. To solve this problem thoroughly, we need to have a shaker for mud. Maintenance, but also in time to find problems at work and give appropriate solutions.
Contact us
Sunny Lee | Sales manager
Basic Knowledge of Mud Gas Separator
Mud Gas Separator
Drilling fluid mud gas separator is also a special equipment for degassing of gas-immersed drilling fluid. It belongs to the category of atmospheric degassing. It is based on the principle of atmospheric degassing. However, it is the primary degassing equipment for treating gas-immersed drilling fluid. The main difference between the degasser and the drilling fluid is that it is mainly used to clear the large bubbles whose diameter is more than 3 mm emitted from annular drilling fluid. Bubble is a kind of expansive gas filled with drilling fluid in a certain section of borehole annulus. Its diameter is about 3-25 mm. These bubbles cause wells to surge and even eject from the surface of the turntable. In addition, the mud gas separator mainly relies on gravity impact to achieve the mud gas separator, while the degasser uses vacuum, turbulence, centrifugation and other principles. The degasser has much less gas handling capacity than the mud gas separator, but clears the gas more thoroughly. Usually there are small bubbles in the drilling fluid treated by the liquid-gas separator. After passing through the vibrating screen, it is necessary to enter the degasser and then carry out conventional degassing.
Types of Mud Gas Separator
There are two types of commonly used mud gas separator.
1. Bottom Cover Type
The bottom of the degassing tank is closed. The drilling fluid is returned to the circulating tank through a U-shaped pipeline. The height of drilling fluid level in degassing tank can be controlled by increasing or decreasing the height of U tube.
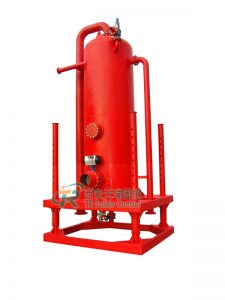
Mud Gas Separator
2. Open Bottom Type
The separator tank is bottomless and the lower part of the separator is submerged in the drilling fluid. The liquid level in the tank is controlled by the depth of submergence at the bottom. This kind of separator, commonly known as “poor boy” abroad, shows its simplicity.
The simplest and most reliable mud gas separator is bottom-sealed. Because its drilling fluid residence height is limited by the liquid level height in the circulating tank. The working pressure of the mud gas separator is equal to the frictional resistance when the free gas is discharged from the discharge pipe. If the friction resistance is greater than the hydrostatic pressure of the drilling fluid column in the separator, it will cause “short circuit” and the gas-immersed drilling fluid without separation will be directly discharged into the drilling fluid circulation tank. The short circuit generated by the separator usually occurs under the condition that a large amount of gas (peak value) appears in the re-gas immersed drilling fluid. This indicates that the separator has insufficient processing capacity.
Application Principle of Liquid-Gas Separator
- The time required for the separation of drilling fluid and gas depends on the performance of drilling fluid. For example, if the viscosity of drilling fluid is high, the separation will be difficult and take a long time.
- Adequate separators and degassing devices must be prepared to treat drilling fluids.
- When the mud gas separator is not in use, the drilling fluid in the equipment should be cleaned and flushed with water. It is strictly forbidden to store the drilling fluid in the separator body, otherwise it will not be able to operate normally after drying up.
- Generally, the surface of the re-drilling fluid tank is required to be level and solid when the separator is installed. And preset anchor bolt pit.
- Lead the exhaust pipe to 60-80 meters away from the wellhead.
- When the slurry inlet is connected with the rotary BOP or throttle manifold, it is necessary to close the sewage butterfly valve, open the slurry outlet butterfly valve and connect the pipeline to the drilling fluid tank.
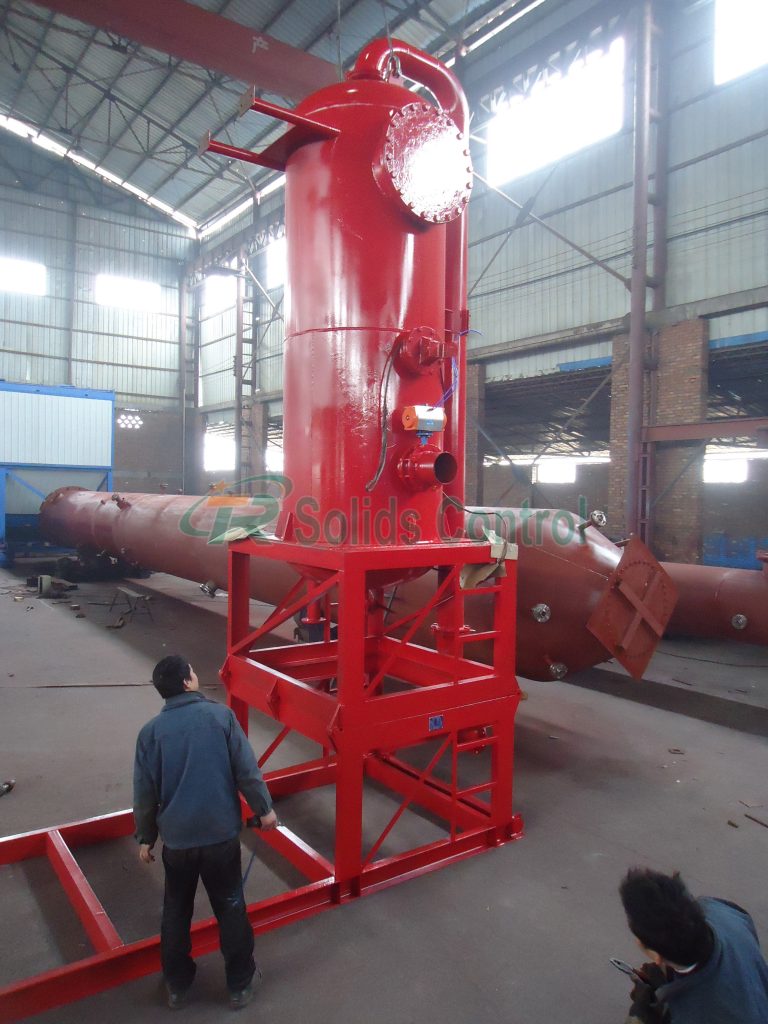
Mud Gas Separator
About Us
Xi’an TianRui Petroleum Machinery Equipment Co.,Ltd(Short name:TR Solids Control) is a solid control equipment manufacturer combined with R&D,sales and service.
We are a technology-based team of passionate people and quality service creativity.
In here, We focus on our career , we have eyes only for this field. We strive for excellence,we make perfection more perfect. Great innovation, do different. Be a most trusted Chinese manufacturing enterprise.
We only have 1 second distance between us.
Contact us
Sunny Lee | Sales manager
TRHDD-250 Mud Recovery System
TRHDD-250 Mud Recovery System
HDD Mud Recovery System is an important part of directional drilling and pipe jacking construction. HDD Mud Recycling System has the function of recycling, purifying and preparing the mud.
HDD mud recycling system is suitable for construction projects with high mud capacity. Mud recovery system purification process is divided into three stages :The first stge of mud shale shaker,the second and the third stage of desander and desilter. Both desander and desilter are equipped with underflow shale shaker to further treat solids discharged from the upper equipment. Necessary mud material is added to the purification slurry through mud preparation device, after stirring uniformly to prepare slurry with qualified recovery performance. This reduces the construction cost greatly and protects the environment effectively.
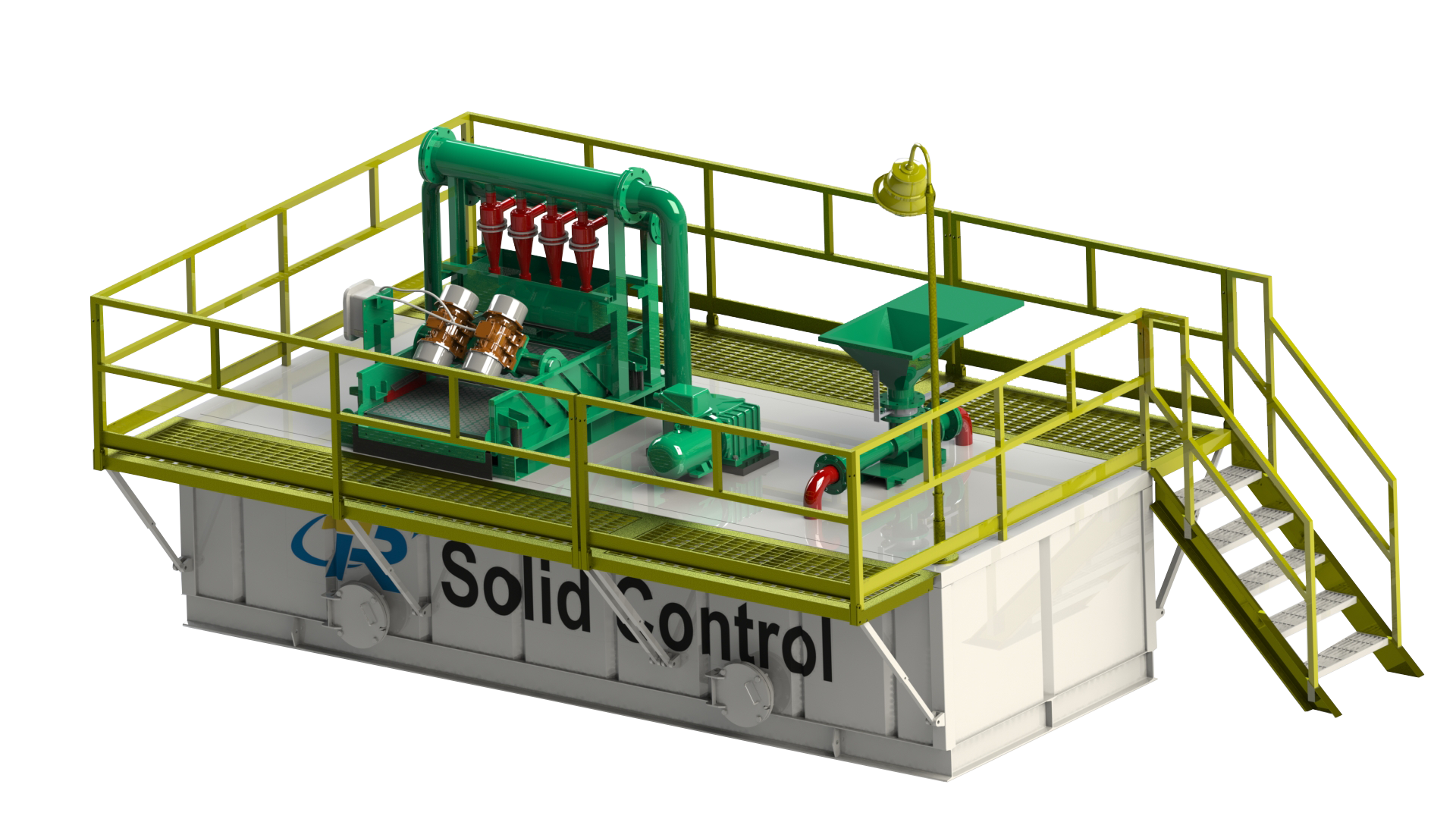
TRHDD-250 Mud Recovery System
Function of HDD Mud Recycling System
HDD Mud Recovery System is to remove the solid particles contained in the mud from bottom of the well,to prepare and store the mud .
In order to maintain low solid phase and performance in line with the performance requirements of construction technology, fine slurry is supplied to mud pump and injected into the well. Thereby improving drilling speed, ensuring the quality of well depth, reducing equipment wear, decreasing drilling cost and reducing the occurrence of construction accidents.
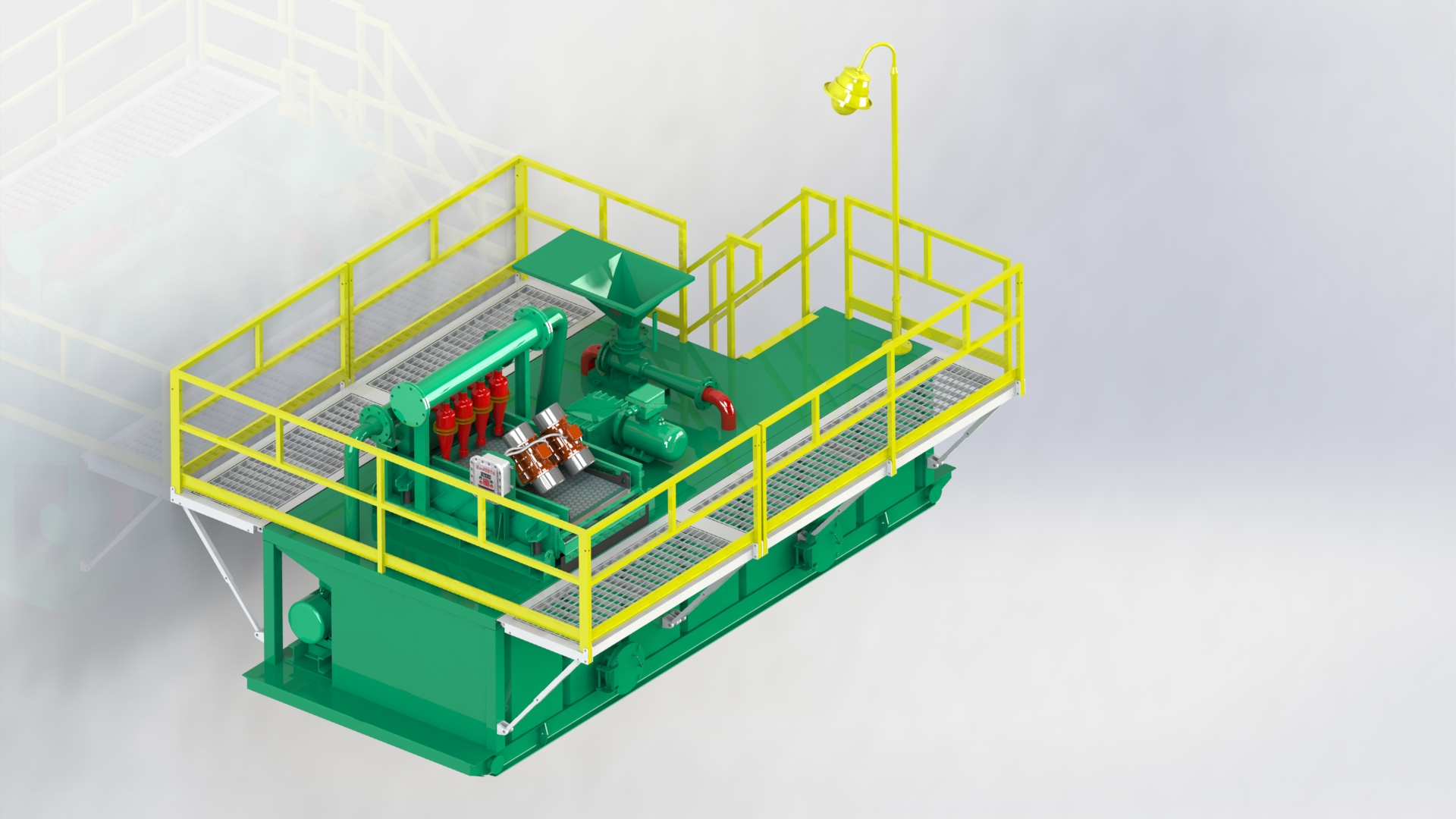
TRHDD-250 Mud Recovery System
250GPM HDD Mud Recycling System Technical Parameters
Model | TRHDD-250 | Supply Pump Model | TRSB4×3-12(15KW) |
System Capacity | 250GPM(60m³/h) | Slurry Pump Model | TRSB4×3-11(11KW) |
Separation Point | 15μm~44μm | Mud Hopper Model | TRSL100 |
Desilter Model | TRCN100-4N | Mud Agitator Model | TRJBQ7.5 |
Vibration intensity | ≤7.5G | Gross Power | 47KW |
Upper Screen Area | 0.875m2 | Total Volume | 5m3 |
Bottom Screen Area | 1.4m2 | Dimension | 4000×2360×3000mm |
Hydrocyclone | 4in | Weight | 6000kg |
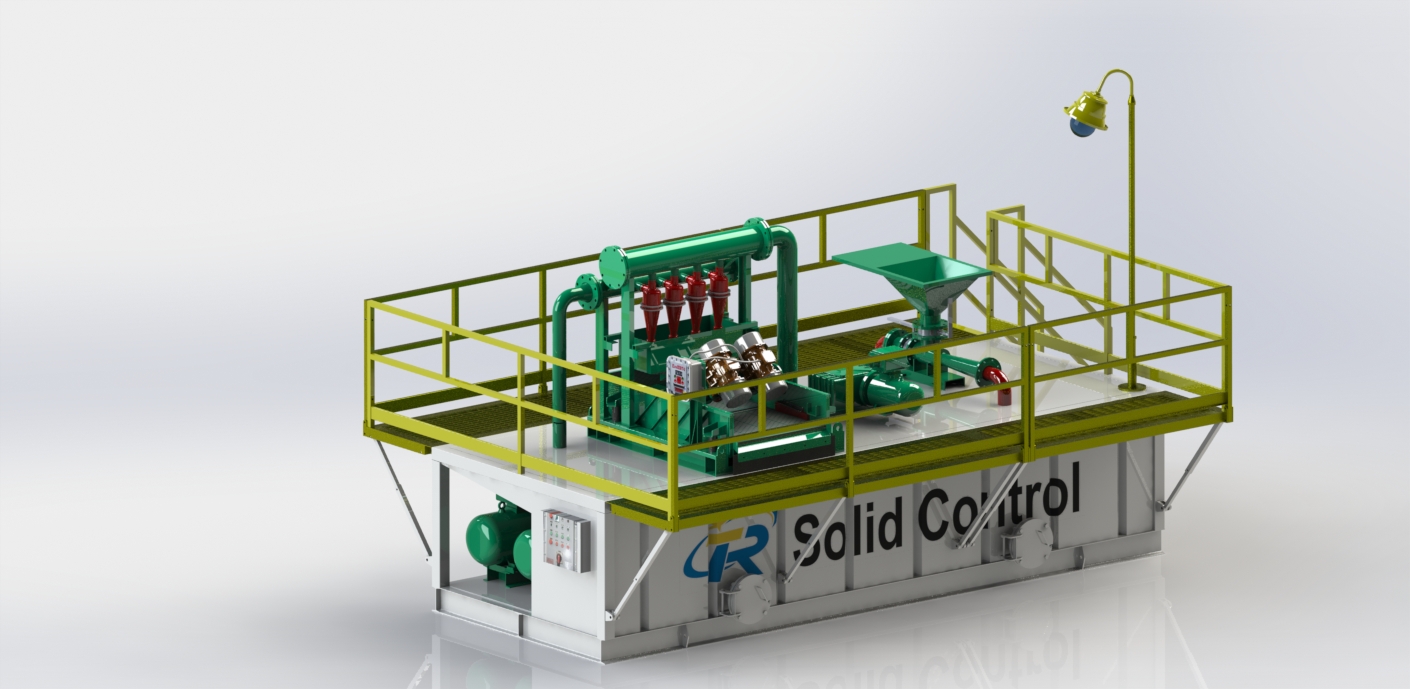
TRHDD-250 Mud Recovery System
We are an exporter of HDD mud recycling system.Our factory approval the API,Solids Control Equipment have the API certification.TR solids control is the designed,selling,production,service and delivery of Chinese mud solids control system manufacturer. We will provide the high quality drilling solids control equipment and best service.Your best hdd mud recycling system start from TR solids control.
Contact Us
sunny@trsolidscontrol.com
M(WhatsApp):+86 13186019379
How to deal with slurry running in mud shale shaker?
Shale shaker, also known as dehydration shaker, dehydration shaker, is a screening equipment for solid-liquid separation, mostly used in coal mines, coal yards, oil and other industries, but some users in the use of Engineering slurry problems. So how to quickly solve this problem users? Now let me make an analysis of this problem.
How to deal with slurry running in mud shale shaker?
1. The mesh number chosen is unreasonable.
The disposal capacity of each shale shaker is 50L/s, because the premise of disposal measurement is to delimit according to national scale: 60 target screens are selected to test the mud with a specific gravity of 1.8, and the mud viscosity is river sand with different grain sizes in the mud. Because of the rapid surface drilling, a large amount of solid phase takes up the useful screen area, so the vibration screen can not be used in the shallow section of the screen. Therefore, in the early stage of drilling, the screen mesh with larger holes should be used, and with the increase of drilling depth, more fine screen mesh should be gradually adopted.
2, formation and mud environmental impact disposal capacity.
In another kind of environment, when drilling into loose sandstone or quicksand layer, sand grains are easily trapped in the screen hole, resulting in screening blockage. It is necessary to test the screen mesh of several different number to reduce the phenomenon of screen plugging.
3, check whether the steering of the motor is accurate.
First, remove the vibrator shield and check whether the rotation of the two parts of the motor is outward to the outside. Secondly, if you turn to fault, please adjust the electrical control box into the power supply in two phase lines. Fault Form 1 (two motors twisting inward) can remove drilling cuttings outward, but it is slow; Fault Form 2 (two motors twisting in the same direction), the vibration force is very small, the foundation does not drain sand or dispose of mud;
4. Check the amplitude of the vibrating screen.
The larger the vibration amplitude, the greater the handling capacity,and the vibration power is adjusted to 90% at the factory. If there is a slurry running environment, the pain block angle can be aligned, and vibration force is 100%. (At this time, mud disposal capacity is increased by only 15%).
5. Is it reasonable to check the distribution of liquid flow on the screen frame?
In the shaker with hooked screen layout, the sieve surfaces on both sides are lower than the center, and the mud flows easily to both sides and runs away. It should be ensured that the mud enters the screen frame from the center. At this point, two options can be adopted. One is to adjust the front spring seat to properly raise the front angle of the screen box; the other is to adjust the position of overturning plate of extension slot to control distribution environment of liquid flow.
Above is the reason and solution of material runaway in mud shaker. If you are interested in shale shaker or encounter difficulties in use, please contact us. TR Solids Control will serve you wholeheartedly.
sunny@trsolidscontrol.com
M(WhatsApp):+86 13186019379